Lifting Requirements and Regulations
Any operation that includes lifting anyone or anything is dangerous make sure you follow the guidance sufficently.
Any operation that involves using equipment to lift something or even someone must understand and follow guidelines. These include the usages of cranes, hoists, gin wheels etc. According to HSE, the law says that all lifting operations involving lifting equipment must be properly planned by a competent person; appropriately supervised, and carried out in a safe manner. Anything that counts as a lifting accessory needs to go through thorough strength testing whilst constantly going through examinations and inspections. All this should be covered in the risk assessment and method statement (RAMS).
The identification and assessment of all lifting equipment needs to be made for every job that may involve lifting being involved. There are two types of lifting operations that need to be considered. They include the very simple and commonplace, where minimal on-the-job planning by trained, competent people may be all that is needed to manage risk to very complex operations, which require sophisticated and detailed planning / records, with very high levels of expert input, monitoring and supervision - undertaken by specially trained personnel. Using the example of a crane being planned for use, it’ll require more sophisticated planning. This is due to the high risk of the operation and the amount of people and supervision it'll take to safely operate the crane. With something at such a high multitude it can get complex. Sticking to the four basics of safety, plan, do, check and act can help keep everything in order.
All examinations and assessments need to follow the requirements of The Lifting Operations and Lifting Equipment Regulations 1998 (LOLER). LOLER created a system of thorough examinations. A thorough examination systematic and detailed examination of the equipment and safety-critical parts, carried out at specified intervals by a competent person (someone who has an advanced amount knowledge and experience dealing with lifting equipment) who must then complete a written report. The report should consist of the date of examination, the date of the next examination and any defects that are/may become a hazard to people.
Thorough examinations are done at multiple times throughout many stages of lifting operation. These include before the use of equipment the first time, after assembly but before usage at location, regularly in service and during exceptional circumstances including damage or non-usage for long periods of time. What each stage requires is further explained by LOLER. What is covered by the thorough examination depends on the competent person. Ideally, damage or deterioration is the main thing that should be covered which either should be made visible or apparent during initial checks and testing of the equipment. Without these examinations lifting operations would be a huge risk to anyone involved in the operation. Although there are no requirements or laws on who the competent person is, it is vital that they are proven to have the knowledge and experience with lifting equipment as the consequences could be catastrophic if not so.
It should be mentioned that LOLER does not cover all lifting equipment. LOLER only applies to operations that are required for work purposes. LOLER operations that may involve public usage. For example, if an occupation has public access that involves a lift/elevator for ease of transport in the building, LOLER does not cover the lift despite still being a type of lifting equipment. These will have their own legislations that they are required to follow. It is important to check LOLER to make sure whether the equipment being used by an operation falls under it. LOLER makes sure everything is carried out in a safe manner and done efficiently with right level of supervision and experience on hand.
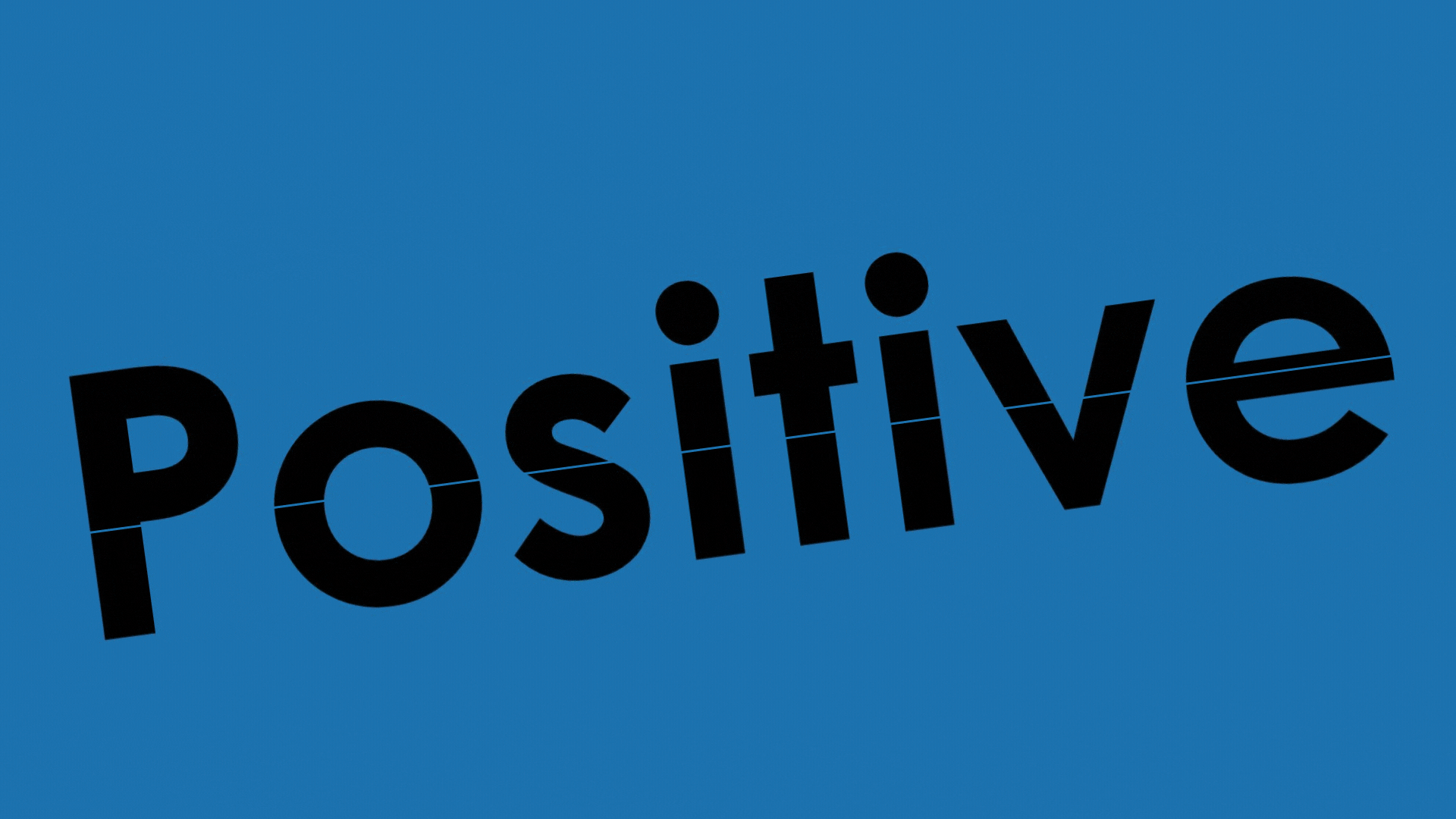
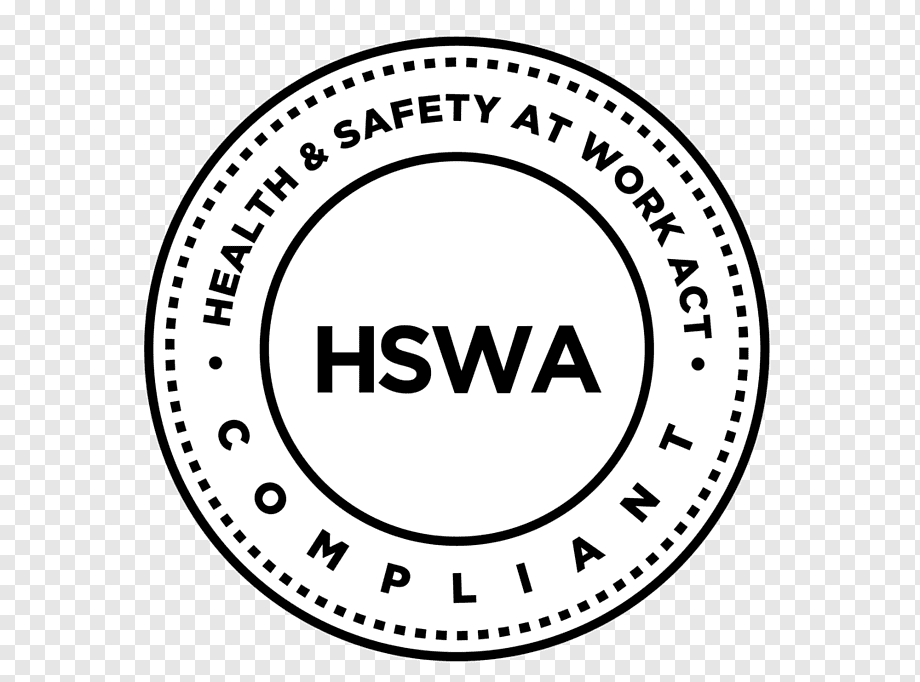
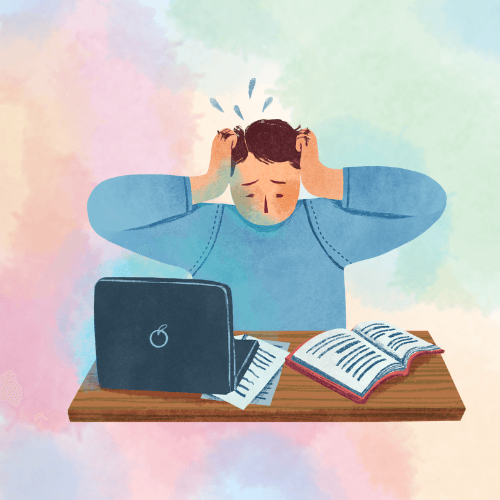